Top 4 Tips to Reduce Tool Deflection in CNC Machining
- Mike Lynch
- Jun 1, 2021
- 4 min read
Thank you to Peter Jacobs of CNC Masters for submitting this great set of suggestions for reducing tool pressure. Every CNC machinist should understand these principles.
Manufacturing parts with accuracy, precision, and sharp-quality finish requires the minimization of tool deflection. Tool deflection happens when the cutting force overpowers the tool's stiffness, which creates a bend.
Tool deflection leads to rapid tool wear and elevates the possibility of tool breakage. Besides boosting part repeatability and quality, preventing tool deflection is economical as it reduces tool replacement frequency and machine downtime.
Tool Deflection and Its Aftermath on CNC Machining
With the CNC machining tool clutched between the chuck in a cantilever position, one end stays locked inside the chuck while the other operating end is free or cantilevered.
When performing CNC machining operations, the tool constantly exerts a force against the workpiece, which results in the workpiece applying a resistive force. The CNC tool takes the brunt of the impact caused by different operational forces. If the tool stiffness does not withstand external forces, it exhibits deflection.
Tool deflection, even by the slightest bit, can result in the following errors in CNC machining:
Depletion of tool life-cycle
Dimensional inaccuracies
Hazardous failure of the workpiece
Rough surface finish or surface damage
Tips To Reduce Tool Deflection in CNC Machining
While tool deflection can lead to catastrophic disasters on a colossal scale, here are some tips that you can follow to alleviate it and ensure high precision in your final product:
1. Build the Tool Core Strength by Altering Diameter
Diameter must be accounted for when calculating deflection. Machinists typically use the cutter diameter when calculating long flute tools, but the core diameter is the dimension that must get considered.
This situation happens because the fluted portion of a tool lacks material in the flute valleys. With a reached tool, the core diameter is employed for calculation until its reached portion, after which it transitions to the neck diameter.
When altering these values, deflection can get minimized to make it negligible for the reached tool. However, this can impact critical dimensions for a long flute tool.
2. Know the Differences Between Long Flute and Long Reach
You can minimize deflection by learning about the differences between a long flute and a long reach tool. The difference in their rigidity occurs due to the core diameter of the tool.
Using more material means higher rigidity, and a smaller flute length means more rigidity and longer life. With each tooling option offering unique benefits and relevant use-cases, it is paramount that you make the appropriate choice for a particular operation.
Applications of a Long Reach Tool
Reached tools are employed when you need to remove material from a gap where the shank would fail to fit in, but a noncutting extension of the cutter diameter would.
The length of reach behind the cutting edge is marginally decreased from the cutter diameter to avoid heeling (rubbing of the noncutting material against the part). Reached tools add to a tool crib owing to their versatility and prolonged tool life.
Applications of a Long Flute Tool
Long flute tools come with longer cut lengths and typically get utilized for providing a seamless wall on the part side or within a slot to complete applications.
The core diameter size remains constant across the cutting length, which leads to greater chances of deflection within a part. This can result in a tapered edge if too little of the cutting edge is involved with a high feed rate.
These tools are efficient when cutting in deep slots. Using HEM can also prove beneficial because of their chip evacuation capabilities, something that reached tools lack.
3. Reduce Overhang Length
The length between the clutching point and the operating tip of a CNC tool is its overhang length. Since the tool gets mounted as a cantilever beam, it must bear bending stress consistently besides external vertical and horizontal forces.
As per the load-stress theory for a cantilever beam, a shorter overhang length leads to a lower bend stress impact. This scenario implies that the minimization of the overhang length of the tool helps decrease tool deflection.
4. Increase Tool Stiffness
CNC machining tools are typically composed of high-speed steel (HSS). High-speed steel helps facilitate machining operations; however, exposure to a higher stress load makes the tools susceptible to deflection.
Carbide tools are one such alternative to HSS tools, considering that carbide is three times more rigid relative to HSS. However, carbide being brittle can be used to reduce deflection. With carbide tools in place, the operator must pay greater attention if the tool snaps as it could compromise their safety.
Final Words
Tool deflection can ruin your tool and scrap your workpiece if left unaccounted before working upon a job. Therefore, it is imperative to lessen the distance from the tool holder to its tip to minimize deflection. You must also emphasize building tool core strength, increasing stiffness, and reducing overhang length.
Besides being careful with your equipment, you must employ a cutting-edge tabletop milling machine to minimize inaccuracies and failure. Standard in-plant CNC training is also necessary to establish that your CNC machines are being implemented appropriately.
About the Author:
Peter Jacobs
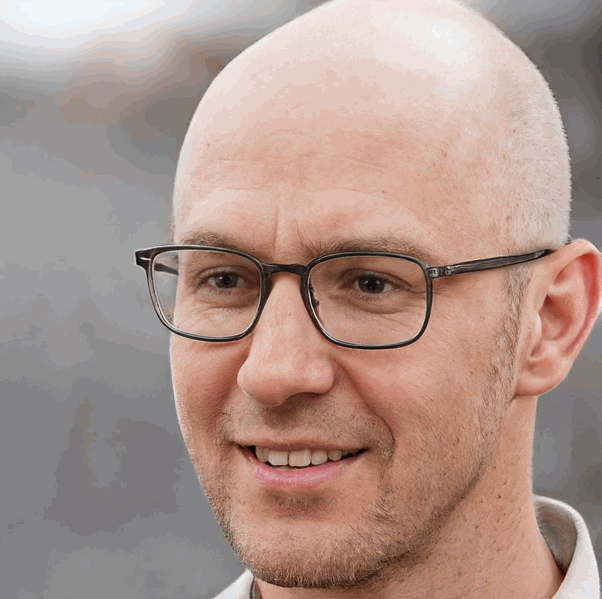
Peter Jacobs is the Senior Director of Marketing at CNC Masters. He is actively involved in manufacturing processes and regularly contributes his insights for various blogs in CNC machining, 3D printing, rapid tooling, injection molding, metal casting, and manufacturing in general.
Comments